Corrosion in the oil and gas industry can have significant negative effects on the equipment, infrastructure, and operations. Some of the effects of corrosion in the oil and gas industry are:
- Loss of production: Corrosion can cause production shutdowns, which can result in significant financial losses for the company. When equipment fails due to corrosion, it can take time to replace or repair, resulting in a temporary loss of production.
- Safety hazards: Corrosion can lead to structural failures of equipment and infrastructure, which can pose serious safety hazards to workers and the environment. Corroded pipes can rupture and cause spills, fires, or explosions, leading to injury or loss of life.
- Environmental damage: Corrosion can cause leaks and spills, which can contaminate soil, water, and air, leading to environmental damage. Corrosion in offshore rigs and pipelines can result in oil spills, which can have long-lasting effects on the marine ecosystem.
- Increased maintenance costs: Corrosion increases the maintenance costs for the company. The frequent replacement or repair of corroded equipment can result in increased downtime and labor costs.
- Reduced equipment lifespan: Corrosion reduces the lifespan of equipment, resulting in the need for frequent replacement or repair. This can result in increased costs for the company and reduced efficiency.
- Reduced efficiency: Corrosion can cause blockages in pipes and reduce the flow rate of oil and gas, resulting in reduced efficiency and lower production rates.
Overall, corrosion in the oil and gas industry can have a significant impact on production, safety, environment, maintenance costs, equipment lifespan, and efficiency. It is, therefore, important to implement effective corrosion prevention and mitigation strategies to minimize its effects.
Loss of production
Corrosion can cause a loss of production in the oil and gas industry. When equipment fails due to corrosion, it can result in unplanned shutdowns, which can halt production and cause significant financial losses for the company. The downtime required to replace or repair the corroded equipment can result in lost production time, which can be very costly.
In some cases, the loss of production due to corrosion can be difficult to predict, as equipment failures may occur suddenly and without warning. This can lead to further delays and increased costs, as companies may need to scramble to find replacement equipment or bring in specialized maintenance crews to address the issue.
Corrosion-related production losses can also have a ripple effect on other areas of the company’s operations. For example, if a pipeline is shut down due to corrosion-related issues, it may impact the entire supply chain, delaying delivery of oil and gas to downstream customers, such as refineries or power plants.
To minimize the impact of corrosion-related production losses, companies in the oil and gas industry must implement effective corrosion prevention and mitigation strategies. This can include regular inspections and maintenance of equipment, the use of corrosion-resistant materials, and the development of contingency plans to address unexpected equipment failures. By taking these steps, companies can reduce the risk of corrosion-related production losses and minimize the impact of any unplanned downtime.
Safety hazards
Corrosion can pose serious safety hazards in the oil and gas industry. When equipment or infrastructure fails due to corrosion, it can lead to structural failures, leaks, spills, fires, or explosions. These incidents can be extremely dangerous for workers and the environment.
Corrosion-related structural failures can lead to the collapse of equipment or infrastructure, causing injury or loss of life. For example, corroded pipelines can rupture and release pressurized oil or gas, resulting in explosions or fires. Corroded storage tanks can also fail and release their contents, causing spills and contamination of soil and water.
In addition to physical damage and injury, corrosion-related incidents can also have long-lasting effects on the environment. For example, oil spills resulting from corroded pipelines or storage tanks can contaminate marine ecosystems and harm wildlife. In some cases, the environmental damage caused by corrosion-related incidents can take years or even decades to fully recover.
To address the safety hazards posed by corrosion, companies in the oil and gas industry must take steps to prevent and mitigate corrosion-related incidents. This can include regular inspections and maintenance of equipment, the use of corrosion-resistant materials, and the development of emergency response plans to address unexpected incidents. By taking these steps, companies can reduce the risk of corrosion-related safety hazards and protect workers and the environment.
Environmental damage
Corrosion in the oil and gas industry can have significant environmental impacts. When equipment or infrastructure fails due to corrosion, it can lead to leaks and spills, which can contaminate soil, water, and air. These incidents can have long-lasting effects on the environment, including damage to ecosystems, harm to wildlife, and threats to human health.
For example, when pipelines or storage tanks corrode, they can rupture and release oil or gas into the surrounding environment. This can cause oil spills that contaminate waterways, harm wildlife, and affect local communities that rely on these resources. Similarly, when offshore rigs corrode, they can leak oil into the ocean, causing damage to marine ecosystems and affecting fishing and tourism industries in the area.
In addition to the direct environmental impacts of corrosion-related incidents, there can also be long-term effects on the environment. For example, when corrosion-related spills are not fully cleaned up, the contaminants can remain in the soil or water for years, leading to ongoing damage to the environment and human health.
To minimize the environmental damage caused by corrosion, companies in the oil and gas industry must take steps to prevent and mitigate corrosion-related incidents. This can include regular inspections and maintenance of equipment, the use of corrosion-resistant materials, and the development of emergency response plans to address unexpected incidents. By taking these steps, companies can reduce the risk of corrosion-related environmental damage and protect the environment and communities in the areas where they operate.
Increased maintenance costs
Corrosion can result in increased maintenance costs in the oil and gas industry. When equipment or infrastructure corrodes, it may require more frequent repairs or replacement. In some cases, the damage caused by corrosion may be irreversible, requiring costly replacement of the affected equipment.
Corrosion-related maintenance costs can include expenses such as cleaning, repairs, replacement of equipment, and ongoing monitoring of corrosion. These costs can add up quickly and can have a significant impact on a company’s bottom line.
In addition to the direct costs of corrosion-related maintenance, there can also be indirect costs associated with the downtime required to address corrosion-related issues. When equipment or infrastructure fails due to corrosion, it can lead to unplanned shutdowns and delays, which can result in lost production time and reduced revenue for the company.
To minimize the increased maintenance costs associated with corrosion, companies in the oil and gas industry must take steps to prevent and mitigate corrosion. This can include regular inspections and maintenance of equipment, the use of corrosion-resistant materials, and the development of contingency plans to address unexpected equipment failures. By taking these steps, companies can reduce the risk of corrosion-related maintenance costs and ensure that their equipment remains in good working order for as long as possible.
Reduced equipment lifespan
Corrosion can significantly reduce the lifespan of equipment in the oil and gas industry. When equipment corrodes, it may become weakened, damaged or even unusable. This can result in unplanned shutdowns, increased maintenance costs, and ultimately, the need for premature replacement of the affected equipment.
Corrosion-related damage can reduce the lifespan of equipment in many ways. For example, corrosion can cause metal components to become brittle and prone to cracking, which can lead to structural failures. Corrosion can also cause leaks or spills, leading to the release of dangerous substances and environmental damage. Additionally, corrosion can cause equipment to become less efficient, reducing its ability to function properly and ultimately leading to its failure.
The reduced lifespan of equipment due to corrosion can have significant financial impacts on companies in the oil and gas industry. Replacing corroded equipment can be costly, and the downtime required to do so can result in lost production time and reduced revenue.
To minimize the impact of corrosion on equipment lifespan, companies in the oil and gas industry must take steps to prevent and mitigate corrosion. This can include the use of corrosion-resistant materials, regular inspections and maintenance of equipment, and the development of contingency plans to address unexpected equipment failures. By taking these steps, companies can reduce the risk of corrosion-related damage and ensure that their equipment remains in good working order for as long as possible, ultimately prolonging its lifespan.
Reduced efficiency
Corrosion can also reduce the efficiency of equipment in the oil and gas industry. When equipment corrodes, it can become less effective and require more energy to perform the same tasks. This can lead to increased energy costs, reduced production efficiency, and ultimately, decreased revenue for the company.
Corrosion-related reductions in equipment efficiency can occur in many ways. For example, corrosion can cause increased friction in machinery, resulting in decreased energy efficiency. Corroded pipelines can also cause increased resistance to fluid flow, resulting in decreased fluid delivery rates.
Reduced efficiency due to corrosion can have significant financial impacts on companies in the oil and gas industry. The decreased efficiency can lead to increased operating costs, as more energy is required to achieve the same level of production. Additionally, the decreased efficiency can result in reduced production rates, leading to decreased revenue for the company.
To minimize the impact of corrosion on equipment efficiency, companies in the oil and gas industry must take steps to prevent and mitigate corrosion. This can include the use of corrosion-resistant materials, regular inspections and maintenance of equipment, and the implementation of corrosion control measures to prevent further corrosion. By taking these steps, companies can reduce the risk of corrosion-related reductions in equipment efficiency and ensure that their equipment remains in good working order for as long as possible.
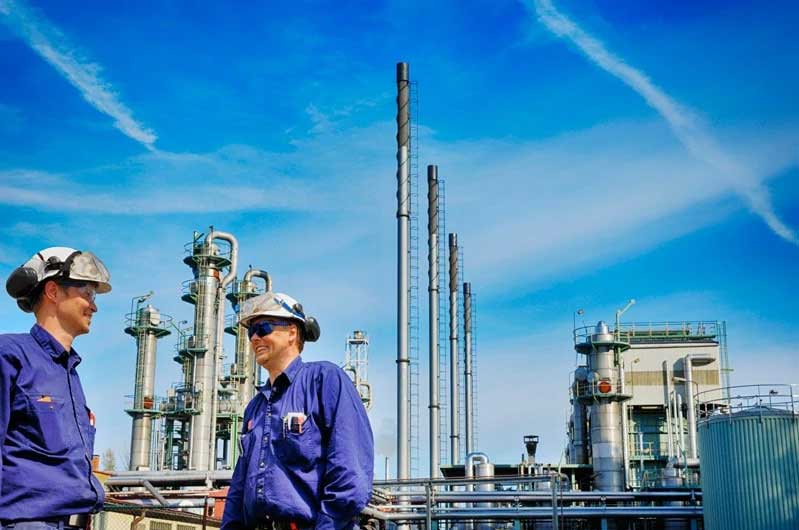
Contact us
Crystal Industrial Syndicate Pvt Ltd.
Phone : +91-22-27563850
Fax: +91-22-67939439
www.crystalindustrial.in
sales@crystalindustrial.in
Crystal Industrial Syndicate from India, manufactures a variety of corrosion coupons for a range of industrial processes. Our world-class corrosion coupons manufactured in India comply with the world’s most stringent certifications. We have clients the world, from Europe and North America to Africa and the Middle East. Please contact us for details about how we can meet your corrosion coupon requirements. Contact us
Copyright © 2023 by Crystal Industrial Syndicate Pvt Ltd. All rights reserved. www.crystalindustrial.in