Why is corrosion coupon testing important in the oil and gas industry?
In the oil and gas industry, corrosion coupon testing is used a lot to check how fast pipelines, storage tanks, and other equipment are rusting. In the oil and gas industry, corrosion coupon testing has a number of benefits, such as:
Improved equipment reliability: By tracking the rate of corrosion, engineers can find places where corrosion is happening and take steps to stop it from spreading. This makes equipment more reliable.
Cost savings: If corrosion is found early, expensive repairs or replacements of equipment can be avoided. This saves a lot of money in the long run.
Corrosion can weaken pipelines and storage tanks, which can make them more likely to leak or spill. Testing corrosion coupons helps to find and stop these potential safety risks.
Better understanding of how corrosion works: Testing corrosion coupons gives useful information about the rate of corrosion, which can be used to learn more about how corrosion works and come up with better ways to stop it.
Compliance with rules: In the oil and gas industry, there are strict rules about how equipment needs to be inspected and kept up. Companies use corrosion coupon testing to make sure they follow these rules and keep a high level of safety.
How corrosion coupon testing gives the oil and gas industry more reliable equipment
In the oil and gas industry, corrosion coupon testing improves the reliability of equipment by giving important information about the rate and cause of corrosion. With this information, engineers can take steps to prevent or stop corrosion, which can make the equipment last longer and make it less likely that it will break down.
By keeping an eye on how fast equipment is rusting, engineers can find areas of concern and take the right steps to stop the rusting. For example, they might decide to switch to a different type of metal or use coatings or inhibitors that stop corrosion in a more aggressive way.
The data from corrosion coupon testing can also be used to improve maintenance schedules and estimate how long equipment will last. This makes it easier to plan and prioritise maintenance tasks, which lowers the chance of unplanned downtime and equipment failure.
Overall, corrosion coupon testing is a good way for the oil and gas industry to improve the reliability of their equipment. By giving engineers important information about the rate and cause of corrosion, they can make smart decisions about how to stop corrosion, which can extend the life of equipment and make it less likely to break.
How corrosion coupon testing can save money in the oil and gas industry
In the oil and gas industry, corrosion coupon testing improves the reliability of equipment by giving important information about the rate and cause of corrosion. With this information, engineers can take steps to prevent or stop corrosion, which can make the equipment last longer and make it less likely that it will break down.
By keeping an eye on how fast equipment is rusting, engineers can find areas of concern and take the right steps to stop the rusting. For example, they might decide to switch to a different type of metal or use coatings or inhibitors that stop corrosion in a more aggressive way.
The data from corrosion coupon testing can also be used to improve maintenance schedules and estimate how long equipment will last. This makes it easier to plan and prioritise maintenance tasks, which lowers the chance of unplanned downtime and equipment failure.
Overall, corrosion coupon testing is a good way for the oil and gas industry to improve the reliability of their equipment. By giving engineers important information about the rate and cause of corrosion, they can make smart decisions about how to stop corrosion, which can extend the life of equipment and make it less likely to break.
How does testing corrosion coupons improve safety in the oil and gas industry?
Corrosion coupon testing makes the oil and gas industry safer by giving important information about how and why equipment corrodes. This information can be used to stop or control corrosion. This can make it less likely that equipment will break down or cause safety problems like leaks, spills, or explosions.
The data from corrosion coupon testing can also be used to improve maintenance schedules and estimate how long equipment will last. This makes it easier to plan and prioritise maintenance tasks, which lowers the chance of unplanned downtime and equipment failure. By cutting down on downtime, companies can boost production and lower the risk of accidents and other problems caused by equipment.
Also, companies can reduce the chance that equipment like pipelines, tanks, and platforms will break down or fall over if they find problem areas and take steps to prevent or control corrosion. This can make workers, contractors, and the public safer as a whole.
In the oil and gas industry as a whole, corrosion coupon testing is a useful way to improve safety. By giving companies important information about the rate and cause of corrosion, they can take steps to prevent or stop it, lowering the risk of equipment failure, downtime, and possible safety hazards.
How does corrosion coupon testing give the oil and gas industry a “better understanding of corrosion mechanisms”?
Corrosion coupon testing helps the oil and gas industry learn more about how corrosion works by giving valuable information about the rate of corrosion and how it happens. This information can be used to figure out what causes corrosion and what the best ways are to stop or control it.
By looking at the corrosion products that form on the coupons, for example, engineers can figure out what kind of corrosion is happening and what causes it, like the presence of certain chemical species, high temperatures, or high stress levels. This information can be used to choose the best materials, coatings, and inhibitors and make equipment more resistant to corrosion as a whole.
Also, by keeping an eye on how fast equipment corrodes, engineers can see if the way it corrodes changes over time and make changes as needed. For example, they might decide to use coatings or inhibitors that stop corrosion more aggressively or switch to a different type of metal.
Overall, corrosion coupon testing is a useful way for the oil and gas industry to learn more about how corrosion works. By giving engineers important information about the rate and cause of corrosion, they can make better decisions about how to stop corrosion and make equipment more resistant to it overall.
How does “Compliance with regulations” come from testing corrosion coupons in the oil and gas industry?
Corrosion coupon testing can offer compliance with regulations in the oil and gas industry by providing important information about the corrosion rate and mechanism of equipment. This information can be used to make sure that equipment is kept in a safe and reliable state and that rules about the environment are followed.
In the oil and gas industry, for example, there are rules that say companies have to keep an eye on and stop corrosion in pipelines and tanks to stop leaks and spills. Testing corrosion coupons can give information about the rate and cause of corrosion. This information can be used to figure out how well corrosion control measures are working and to make sure that the equipment is being maintained in accordance with regulations.
Also, corrosion coupon testing can tell you important things about how long a piece of equipment has left to work. You can use this information to plan maintenance and make sure that equipment is replaced before it becomes unsafe or stops working. This helps make sure that equipment is used in a safe and responsible way and that companies are following regulations and industry standards.
Overall, corrosion coupon testing is a good way to make sure that the oil and gas industry is following the rules. By giving important information about how and why equipment corrodes, companies can take preventative steps to stop or slow corrosion, make sure equipment works safely and reliably, and meet regulations and industry standards.
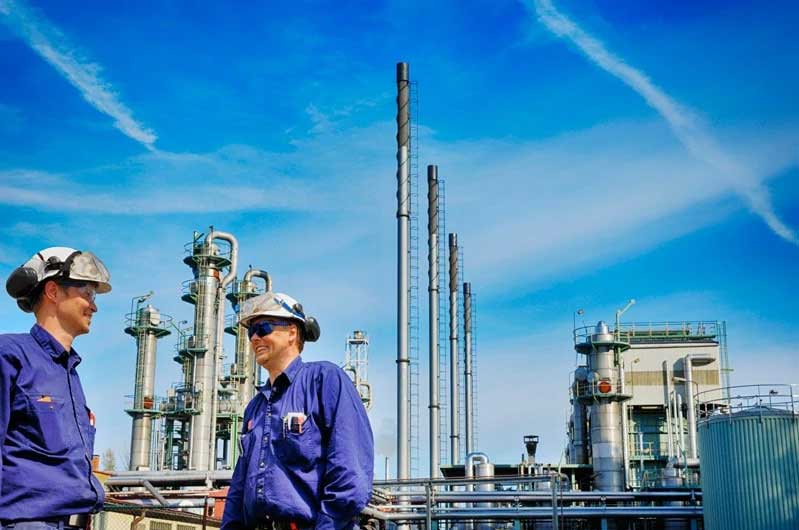
Contact us
Crystal Industrial Syndicate Pvt Ltd.
Phone : +91-22-27563850
Fax: +91-22-67939439
www.crystalindustrial.in
sales@crystalindustrial.in
Crystal Industrial Syndicate from India, manufactures a variety of corrosion coupons for a range of industrial processes. Our world-class corrosion coupons manufactured in India comply with the world’s most stringent certifications. We have clients the world, from Europe and North America to Africa and the Middle East. Please contact us for details about how we can meet your corrosion coupon requirements. Contact us
Copyright © 2023 by Crystal Industrial Syndicate Pvt Ltd. All rights reserved. www.crystalindustrial.in