Corrosion coupons are widely used in the oil and gas industry to monitor and control corrosion in various components of oil and gas production, processing, and transportation systems. Here are some key applications of corrosion coupons in the oil and gas industry:
- Pipeline Monitoring: Corrosion coupons can be used to monitor corrosion rates in pipelines, which is essential to prevent leaks and other types of failures. Coupons can be installed in various locations along the pipeline to monitor localized corrosion rates and to identify areas that may require additional protection or repair.
- Storage Tank Monitoring: Storage tanks are vulnerable to corrosion due to the presence of moisture, contaminants, and impurities. Corrosion coupons can be installed in storage tanks to monitor the corrosion rate and to ensure that the tank remains in good condition.
- Oil Well Tubing Monitoring: Corrosion in oil well tubing can lead to a decrease in production rates, as well as an increase in maintenance costs. Corrosion coupons can be used to monitor corrosion rates in tubing, and to identify areas that require additional protection or repair.
- Offshore Platform Monitoring: Offshore platforms are exposed to harsh environmental conditions that can accelerate corrosion rates. Corrosion coupons can be installed in various locations on offshore platforms to monitor corrosion rates and to identify areas that require additional protection or repair.
- Corrosion Inhibitor Effectiveness: Corrosion inhibitors are commonly used in the oil and gas industry to reduce corrosion rates. Corrosion coupons can be used to test the effectiveness of corrosion inhibitors in specific applications.
Overall, corrosion coupons play a vital role in the oil and gas industry by providing a cost-effective and accurate method for monitoring and controlling corrosion in various components of oil and gas production, processing, and transportation systems. By monitoring corrosion rates and identifying areas that require additional protection or repair, corrosion coupons help to ensure safe and reliable operation of oil and gas facilities.
Pipeline Monitoring
Pipeline monitoring is a critical application of corrosion coupons in the oil and gas industry. Pipelines are essential for transporting oil and gas from production sites to processing facilities and distribution centers. However, pipelines are also vulnerable to corrosion due to exposure to various factors such as moisture, contaminants, and impurities. Corrosion can weaken the pipeline walls, causing leaks and other types of failures.
To prevent corrosion and ensure the safe operation of pipelines, corrosion coupons can be installed at various locations along the pipeline. These coupons provide a cost-effective method for monitoring corrosion rates and identifying areas that require additional protection or repair.
The coupons are typically installed at locations where localized corrosion is expected to occur, such as at bends, welds, or areas of stress concentration. The coupons are made of the same materials as the pipeline, and they are installed in the same orientation as the pipeline to ensure accurate data collection.
The coupons are typically left in place for a predetermined amount of time, usually several months. After the coupons are retrieved, they are analyzed to determine the corrosion rate and the extent of corrosion on the coupon surface. The data collected from the coupons can be used to identify areas that require additional protection or repair, and to adjust corrosion prevention and control strategies as needed.
Overall, pipeline monitoring using corrosion coupons is a cost-effective and accurate method for preventing pipeline failures and ensuring the safe and reliable transport of oil and gas. By identifying areas that require additional protection or repair, pipeline monitoring using corrosion coupons helps to prevent leaks and other types of failures, reducing the risk of environmental damage and improving operational efficiency.
Storage Tank Monitoring
Storage tank monitoring is another important application of corrosion coupons in the oil and gas industry. Storage tanks are used to store various types of fluids, including crude oil, refined products, and chemicals. However, storage tanks are vulnerable to corrosion due to the presence of moisture, contaminants, and impurities.
Corrosion coupons can be installed in storage tanks to monitor the corrosion rate and to ensure that the tank remains in good condition. The coupons are typically installed on the tank walls at various locations to monitor localized corrosion rates. The coupons are made of the same materials as the tank walls and are installed in the same orientation to ensure accurate data collection.
The coupons are left in place for a predetermined amount of time, typically several months. After the coupons are retrieved, they are analyzed to determine the corrosion rate and the extent of corrosion on the coupon surface. The data collected from the coupons can be used to adjust corrosion prevention and control strategies as needed, and to identify areas of the tank that require additional protection or repair.
In addition to corrosion monitoring, storage tank monitoring using corrosion coupons can also be used to assess the effectiveness of corrosion inhibitors. Corrosion inhibitors are commonly used in the oil and gas industry to reduce corrosion rates. Corrosion coupons can be used to test the effectiveness of corrosion inhibitors in specific applications.
Overall, storage tank monitoring using corrosion coupons is an essential part of corrosion prevention and control in the oil and gas industry. By monitoring corrosion rates and identifying areas that require additional protection or repair, corrosion coupons help to ensure the safe and reliable storage of oil and gas products.
Oil Well Tubing Monitoring
Oil well tubing monitoring is a crucial application of corrosion coupons in the oil and gas industry. Corrosion in oil well tubing can lead to a decrease in production rates, as well as an increase in maintenance costs. Corrosion coupons can be installed in oil well tubing to monitor corrosion rates and to identify areas that require additional protection or repair.
The coupons are typically installed in the same orientation as the tubing to ensure accurate data collection. They are made of the same materials as the tubing and are installed at various locations along the tubing to monitor localized corrosion rates.
The coupons are left in place for a predetermined amount of time, typically several months. After the coupons are retrieved, they are analyzed to determine the corrosion rate and the extent of corrosion on the coupon surface. The data collected from the coupons can be used to adjust corrosion prevention and control strategies as needed, and to identify areas of the tubing that require additional protection or repair.
In addition to corrosion monitoring, oil well tubing monitoring using corrosion coupons can also be used to test the effectiveness of corrosion inhibitors. Corrosion inhibitors are commonly used in the oil and gas industry to reduce corrosion rates. Corrosion coupons can be used to test the effectiveness of corrosion inhibitors in specific applications.
Overall, oil well tubing monitoring using corrosion coupons is an essential part of corrosion prevention and control in the oil and gas industry. By monitoring corrosion rates and identifying areas that require additional protection or repair, corrosion coupons help to ensure the safe and efficient production of oil and gas.
Offshore Platform Monitoring
Offshore platform monitoring is a critical application of corrosion coupons in the oil and gas industry. Offshore platforms are exposed to a harsh marine environment, and they are vulnerable to corrosion due to the presence of saltwater, high humidity, and contaminants.
Corrosion coupons can be installed on offshore platforms to monitor the corrosion rate and to identify areas that require additional protection or repair. The coupons are typically installed at various locations on the platform, including on the legs, deck, and other areas that are exposed to the marine environment.
The coupons are made of the same materials as the platform and are installed in the same orientation to ensure accurate data collection. The coupons are left in place for a predetermined amount of time, typically several months. After the coupons are retrieved, they are analyzed to determine the corrosion rate and the extent of corrosion on the coupon surface.
The data collected from the coupons can be used to adjust corrosion prevention and control strategies as needed, and to identify areas of the platform that require additional protection or repair. In addition to corrosion monitoring, offshore platform monitoring using corrosion coupons can also be used to assess the effectiveness of corrosion inhibitors.
Overall, offshore platform monitoring using corrosion coupons is an essential part of corrosion prevention and control in the oil and gas industry. By monitoring corrosion rates and identifying areas that require additional protection or repair, corrosion coupons help to ensure the safe and reliable operation of offshore platforms, reducing the risk of environmental damage and improving operational efficiency.
Corrosion Inhibitor Effectiveness
Corrosion inhibitors are chemical compounds that are added to fluids or applied to surfaces to reduce the rate of corrosion. The effectiveness of corrosion inhibitors can be assessed using corrosion coupons in a variety of applications within the oil and gas industry, including pipeline monitoring, storage tank monitoring, and oil well tubing monitoring.
Corrosion coupons are installed in the same environment as the fluid or surface being protected, and the corrosion rate on the coupon is monitored over a predetermined amount of time. This provides a way to determine the effectiveness of the corrosion inhibitor in that specific application.
Corrosion coupons can also be used to test different corrosion inhibitors in the same application to determine which inhibitor is the most effective. This can help oil and gas companies choose the best inhibitor for a particular application and optimize their corrosion prevention and control strategies.
Overall, assessing the effectiveness of corrosion inhibitors using corrosion coupons is a crucial part of corrosion prevention and control in the oil and gas industry. By identifying the most effective inhibitors, companies can reduce corrosion rates, improve operational efficiency, and extend the lifespan of their equipment and infrastructure.
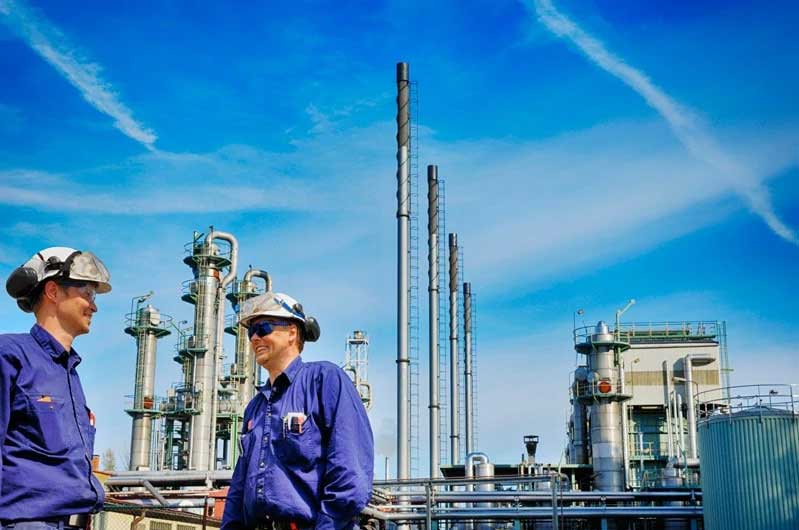
Contact us
Crystal Industrial Syndicate Pvt Ltd.
Phone : +91-22-27563850
Fax: +91-22-67939439
www.crystalindustrial.in
sales@crystalindustrial.in
Crystal Industrial Syndicate from India, manufactures a variety of corrosion coupons for a range of industrial processes. Our world-class corrosion coupons manufactured in India comply with the world’s most stringent certifications. We have clients the world, from Europe and North America to Africa and the Middle East. Please contact us for details about how we can meet your corrosion coupon requirements. Contact us
Copyright © 2023 by Crystal Industrial Syndicate Pvt Ltd. All rights reserved. www.crystalindustrial.in