What are the electrochemical factors that affect corrosion coupon testing?
Electrochemical factors that affect corrosion coupon testing include:
- Electrode potential: The potential of the coupon material determines the rate of corrosion.
- Electrolyte composition: The composition of the surrounding electrolyte (e.g. pH, chloride concentration) affects the corrosion rate.
- Surface area: The larger the surface area of the coupon, the faster the corrosion rate.
- Current density: The rate of corrosion is proportional to the current density flowing through the coupon material.
- Temperature: The temperature of the electrolyte affects the rate of corrosion.
- Hydrodynamic conditions: The flow of the electrolyte over the coupon surface affects the corrosion rate.
- Electrode material: The type of material used for the coupon affects the corrosion rate.
- Presence of inhibitors: The presence of corrosion inhibitors can reduce the corrosion rate.
How Electrode potential affects Corrosion Coupon testing
These factors need to be controlled and considered when interpreting the results of corrosion coupon tests.
Electrode potential, also known as electrochemical potential, affects corrosion coupon testing by determining the corrosion rate of the coupon material. In corrosion coupon testing, the corrosion coupon manufactured in India is used as a working electrode and its potential is measured relative to a reference electrode.
The corrosion rate of the coupon manufactured in India is related to the electrode potential, with more negative potentials resulting in higher corrosion rates and more positive potentials resulting in lower corrosion rates. Factors such as the composition of the electrolyte, the presence of corrosion inhibitors, and the temperature of the test environment can all affect the electrode potential and, as a result, the corrosion rate.
Therefore, it is important to carefully control and monitor the electrode potential during corrosion coupon tests to obtain accurate results and to determine the influence of different factors on the corrosion rate.
How Electrolyte composition affects Corrosion Coupon testing
- Corrosion rate: The composition of the electrolyte can greatly affect the corrosion rate of the coupon material, with different electrolyte compositions leading to different corrosion rates.
- Electrode potential: The composition of the electrolyte can affect the electrode potential, which in turn affects the corrosion rate.
- Presence of inhibitors: The presence of inhibitors in the electrolyte can affect the corrosion rate by slowing down or inhibiting corrosion.
- Contamination: The presence of impurities in the electrolyte can affect the corrosion rate by altering the composition of the electrolyte.
- pH: The pH of the electrolyte can affect the corrosion rate by altering the availability of ions in solution.
The composition of the electrolyte affects corrosion coupon testing in the following ways:
Therefore, it is important to carefully control and monitor the composition of the electrolyte during corrosion coupon tests to obtain accurate results and to determine the influence of different factors on the corrosion rate.
How Surface area affects Corrosion Coupon testing
Surface area affects corrosion coupon testing in the following ways:
- Corrosion rate: The surface area of the coupon can affect the corrosion rate, with larger surface areas leading to higher corrosion rates and smaller surface areas leading to lower corrosion rates.
- Electrode potential: The surface area of the coupon can affect the electrode potential, which in turn affects the corrosion rate.
- Availability of electrolyte: The surface area of the coupon affects the availability of the electrolyte, which can influence the corrosion rate.
- Protective coatings: The surface area of the coupon affects the effectiveness of protective coatings, with larger surface areas requiring more protective coating to effectively prevent corrosion.
Therefore, it is important to carefully control and monitor the surface area of the coupon during corrosion coupon tests to obtain accurate results and to determine the influence of different factors on the corrosion rate.
How Current density affects Corrosion Coupon testing
Current density affects corrosion coupon testing in the following ways:
- Corrosion rate: The current density passing through the coupon can affect the corrosion rate, with higher current densities leading to higher corrosion rates and lower current densities leading to lower corrosion rates.
- Electrode potential: The current density passing through the coupon can affect the electrode potential, which in turn affects the corrosion rate.
- Oxygen availability: The current density passing through the coupon can affect the availability of oxygen, which can influence the corrosion rate.
- Protective coatings: The current density passing through the coupon can affect the effectiveness of protective coatings, with higher current densities requiring more effective protective coatings to prevent corrosion.
Therefore, it is important to carefully control and monitor the current density during corrosion coupon tests to obtain accurate results and to determine the influence of different factors on the corrosion rate.
How Temperature affects Corrosion Coupon testing
Temperature affects corrosion coupon testing in the following ways:
- Corrosion rate: The temperature of the test environment can greatly affect the corrosion rate of the coupon material, with higher temperatures leading to higher corrosion rates and lower temperatures leading to lower corrosion rates.
- Electrode potential: The temperature of the test environment can affect the electrode potential, which in turn affects the corrosion rate.
- Electrolyte composition: The temperature of the test environment can affect the composition of the electrolyte, which can influence the corrosion rate.
- Protective coatings: The temperature of the test environment can affect the effectiveness of protective coatings, with higher temperatures requiring more effective protective coatings to prevent corrosion.
Therefore, it is important to carefully control and monitor the temperature during corrosion coupon tests to obtain accurate results and to determine the influence of different factors on the corrosion rate.
How Hydrodynamic conditions affect Corrosion Coupon testing
Hydrodynamic conditions, such as flow velocity, turbulence, and fluid flow patterns, affect corrosion coupon testing in the following ways:
- Corrosion rate: Hydrodynamic conditions can greatly affect the corrosion rate of the coupon material, with higher flow velocity, turbulence, and fluid flow leading to higher corrosion rates and lower flow velocity, turbulence, and fluid flow leading to lower corrosion rates.
- Electrode potential: Hydrodynamic conditions can affect the electrode potential, which in turn affects the corrosion rate.
- Electrolyte composition: Hydrodynamic conditions can affect the composition of the electrolyte, which can influence the corrosion rate.
- Protective coatings: Hydrodynamic conditions can affect the effectiveness of protective coatings, with high flow velocity, turbulence, and fluid flow requiring more effective protective coatings to prevent corrosion.
Therefore, it is important to carefully control and monitor hydrodynamic conditions during corrosion coupon tests to obtain accurate results and to determine the influence of different factors on the corrosion rate.
How Electrode material affects Corrosion Coupon testing
The electrode material used in corrosion coupon testing can greatly affect the test results, as it can influence the following factors:
- Corrosion rate: Different electrode materials can have different corrosion rates, which can affect the overall corrosion rate of the coupon material.
- Electrode potential: Different electrode materials can have different electrode potentials, which can affect the overall corrosion rate of the coupon material.
- Protective coatings: Different electrode materials may require different protective coatings to prevent corrosion, and the effectiveness of protective coatings can be influenced by the electrode material.
Therefore, it is important to carefully select and control the electrode material used during corrosion coupon tests to obtain accurate results and to determine the influence of different factors on the corrosion rate.
How Presence of inhibitors affects Corrosion Coupon testing
The presence of inhibitors, such as corrosion inhibitors, can greatly affect corrosion coupon testing, as they can influence the following factors:
- Corrosion rate: Corrosion inhibitors can slow down the corrosion rate of the coupon material, making the results of the test different from those obtained in the absence of inhibitors.
- Electrode potential: Corrosion inhibitors can affect the electrode potential, which in turn affects the corrosion rate.
- Electrolyte composition: Corrosion inhibitors can affect the composition of the electrolyte, which can influence the corrosion rate.
Therefore, it is important to carefully control and monitor the presence of inhibitors during corrosion coupon tests to obtain accurate results and to determine the influence of different factors on the corrosion rate. Additionally, it is important to consider the effects of inhibitors when interpreting and comparing the results of different corrosion coupon tests.
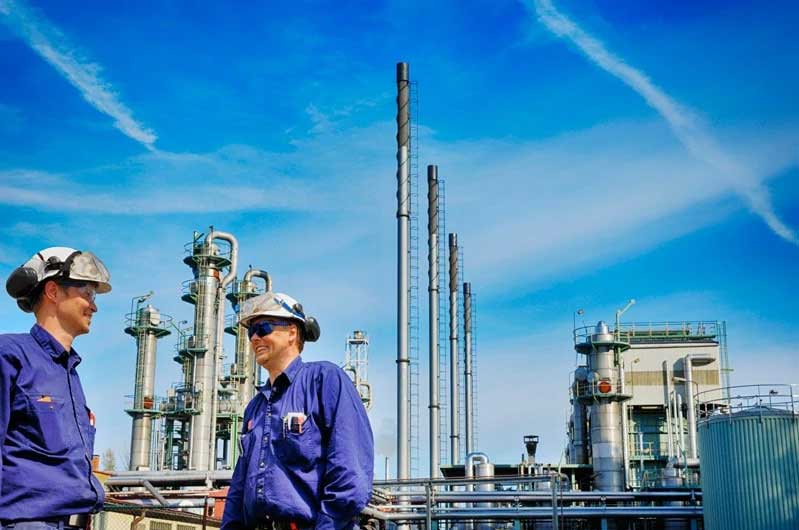
Contact us
Crystal Industrial Syndicate Pvt Ltd.
Telephone : +91-22-27563850 |
Telefax : +91-22-67939439
sales@crystalindustrial.in
Crystal Industrial Syndicate from India, manufactures a variety of corrosion coupons in India for a range of industrial processes. Our world-class corrosion coupons manufactured in India comply with the world’s most stringent certifications. We have clients the world, from Europe and North America to Africa and the Middle East. Please contact us for details about how we can meet your corrosion coupon requirements. Contact us
Copyright © 2023 by Crystal Industrial Syndicate Pvt Ltd. All rights reserved. www.crystalindustrial.in