Corrosion coupons are widely used in power plants to monitor and control corrosion in various components and systems. The following are some of the key applications of corrosion coupons in power plants.
- Boiler and steam system monitoring: Corrosion coupons can be used to monitor corrosion rates in boilers, steam lines, and other components of the steam system. The coupons are typically installed in the same orientation as the equipment and left in place for a predetermined amount of time. After the coupons are retrieved, they are analyzed to determine the corrosion rate and the extent of corrosion on the coupon surface. This information can be used to optimize the chemical treatment of the water and to adjust the operational parameters of the system.
- Cooling water system monitoring: Corrosion coupons can be used to monitor corrosion rates in cooling water systems, including the cooling towers, heat exchangers, and condensers. The coupons are typically installed in the same manner as in boiler and steam system monitoring and left in place for a predetermined amount of time. The data collected from the coupons can be used to optimize the chemical treatment of the water and to adjust the operational parameters of the system.
- Turbine monitoring: Corrosion coupons can be used to monitor corrosion rates in the turbines, including the blades, casing, and other components. The coupons are typically installed in the same orientation as the equipment and left in place for a predetermined amount of time. After the coupons are retrieved, they are analyzed to determine the corrosion rate and the extent of corrosion on the coupon surface. This information can be used to optimize the chemical treatment of the water and to adjust the operational parameters of the system.
- Fuel gas system monitoring: Corrosion coupons can be used to monitor corrosion rates in the fuel gas system, including the gas turbines, compressors, and pipelines. The coupons are typically installed in the same orientation as the equipment and left in place for a predetermined amount of time. After the coupons are retrieved, they are analyzed to determine the corrosion rate and the extent of corrosion on the coupon surface. This information can be used to optimize the chemical treatment of the fuel gas and to adjust the operational parameters of the system.
By using corrosion coupons in power plants, operators can optimize their corrosion prevention and control strategies, reduce maintenance costs, extend the lifespan of their equipment, and ensure the reliable and efficient operation of the power plant.
Boiler and steam system monitoring
Boiler and steam system monitoring is a crucial application of corrosion coupons in power plants. Corrosion coupons are used to monitor the corrosion rate and the extent of corrosion in the boilers, steam lines, and other components of the steam system.
To monitor the corrosion rate, coupons are installed in the same orientation as the equipment and left in place for a predetermined amount of time. The coupons are then retrieved and analyzed to determine the extent of corrosion on the coupon surface. This information can be used to optimize the chemical treatment of the water and to adjust the operational parameters of the system.
By monitoring and controlling the corrosion rate in the boiler and steam system, power plant operators can reduce maintenance costs, extend the lifespan of their equipment, and ensure the reliable and efficient operation of the power plant. Moreover, the use of corrosion coupons can help ensure the safety of the equipment and personnel by identifying areas of high corrosion rates that may lead to equipment failure or leaks.
Cooling water system monitoring
Cooling water system monitoring is another important application of corrosion coupons in power plants. Corrosion coupons are used to monitor the corrosion rate and extent of corrosion in the cooling towers, heat exchangers, and condensers.
To monitor the corrosion rate, coupons are installed in the same manner as in boiler and steam system monitoring and left in place for a predetermined amount of time. The coupons are then retrieved and analyzed to determine the extent of corrosion on the coupon surface. This information can be used to optimize the chemical treatment of the water and to adjust the operational parameters of the system.
By monitoring and controlling the corrosion rate in the cooling water system, power plant operators can prevent the formation of corrosion products that can cause fouling and reduce heat transfer efficiency. This, in turn, can reduce energy consumption and maintenance costs, extend the lifespan of the equipment, and ensure the reliable and efficient operation of the power plant.
Turbine monitoring
Turbine monitoring is another important application of corrosion coupons in power plants. Corrosion coupons are used to monitor the extent of corrosion on the surface of turbine components such as blades, rotors, and casings.
To monitor the corrosion rate, coupons are installed in the same manner as in boiler and steam system monitoring and left in place for a predetermined amount of time. The coupons are then retrieved and analyzed to determine the extent of corrosion on the coupon surface. This information can be used to optimize the chemical treatment of the water and to adjust the operational parameters of the system.
By monitoring and controlling the corrosion rate in the turbine components, power plant operators can prevent equipment failure, reduce maintenance costs, and ensure the reliable and efficient operation of the power plant. Moreover, the use of corrosion coupons can help ensure the safety of the equipment and personnel by identifying areas of high corrosion rates that may lead to equipment failure or leaks.
Fuel gas system monitoring
Fuel gas system monitoring is another application of corrosion coupons in power plants. Corrosion coupons are used to monitor the extent of corrosion in the fuel gas system, which includes the gas supply lines, valves, and associated equipment.
To monitor the corrosion rate, coupons are installed in the same manner as in boiler and steam system monitoring and left in place for a predetermined amount of time. The coupons are then retrieved and analyzed to determine the extent of corrosion on the coupon surface. This information can be used to optimize the chemical treatment of the gas and to adjust the operational parameters of the system.
By monitoring and controlling the corrosion rate in the fuel gas system, power plant operators can prevent equipment failure, reduce maintenance costs, and ensure the reliable and efficient operation of the power plant. Additionally, monitoring the corrosion rate of the fuel gas system can help ensure the safety of the equipment and personnel by identifying areas of high corrosion rates that may lead to equipment failure or leaks, which could potentially result in an accident.
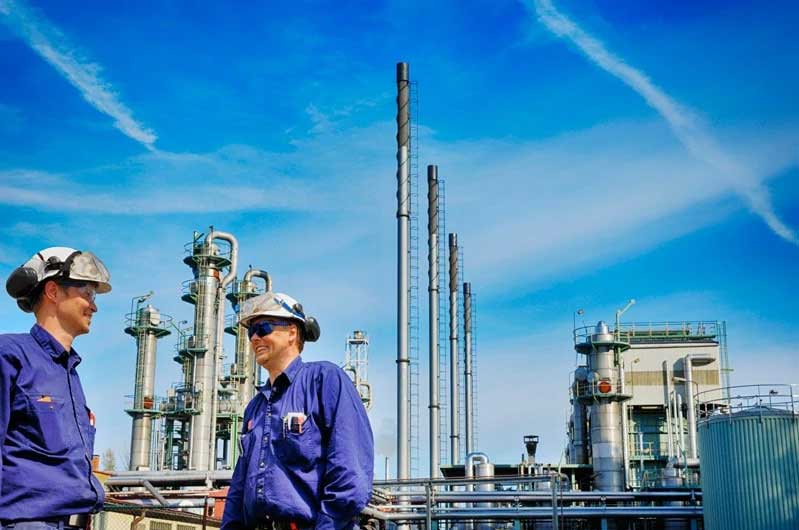
Contact us
Crystal Industrial Syndicate Pvt Ltd.
Phone : +91-22-27563850
Fax: +91-22-67939439
www.crystalindustrial.in
sales@crystalindustrial.in
Crystal Industrial Syndicate from India, manufactures a variety of corrosion coupons for a range of industrial processes. Our world-class corrosion coupons manufactured in India comply with the world’s most stringent certifications. We have clients the world, from Europe and North America to Africa and the Middle East. Please contact us for details about how we can meet your corrosion coupon requirements. Contact us
Copyright © 2023 by Crystal Industrial Syndicate Pvt Ltd. All rights reserved. www.crystalindustrial.in