Electrochemical impedance spectroscopy
Electrochemical impedance spectroscopy (EIS) is a widely used technique for monitoring corrosion rates in the oil and gas industry. EIS involves measuring the electrical response of a metal coupon to a small sinusoidal electrical potential, over a range of frequencies. The resulting impedance spectrum can be analyzed to determine the corrosion rate and the corrosion mechanism.
The principle behind this method is that as a metal corrodes, its electrical properties change, which affects the impedance response of the metal. The impedance spectrum is then analyzed using mathematical models to determine the corrosion rate and mechanism.
EIS is a powerful technique for monitoring corrosion rates, as it can provide detailed information on the corrosion mechanism and the effects of environmental factors such as temperature, pressure, and composition. This method can detect both uniform and localized corrosion, including pitting and crevice corrosion, which may not be detected by other techniques.
However, EIS is a complex and time-consuming technique that requires specialized equipment and expertise. The interpretation of the data requires mathematical modeling, which can be challenging and may require significant experience to accurately interpret the results.
Despite these limitations, EIS is a valuable technique for monitoring corrosion rates in the oil and gas industry. It can be used to optimize corrosion control strategies, to evaluate the performance of corrosion inhibitors and other protective coatings, and to provide insights into the mechanisms of corrosion. EIS is often used in combination with other corrosion monitoring techniques, such as weight loss measurement and polarization resistance measurement, to provide a more comprehensive understanding of the corrosion process.
Hydrogen permeation measurement
Hydrogen permeation measurement is a specialized technique for monitoring hydrogen-induced cracking in the oil and gas industry. This method involves exposing a metal coupon to a corrosive environment containing hydrogen, and measuring the amount of hydrogen that diffuses into the metal. The amount of hydrogen uptake is proportional to the risk of hydrogen-induced cracking, and can be used to evaluate the performance of materials and coatings in environments containing hydrogen.
The principle behind this method is that as a metal is exposed to a hydrogen-containing environment, some of the hydrogen will diffuse into the metal, causing hydrogen embrittlement and increasing the risk of cracking. The amount of hydrogen that diffuses into the metal is dependent on factors such as the material properties, the environmental conditions, and the presence of protective coatings.
Hydrogen permeation measurement is a complex and specialized technique that requires specialized equipment and expertise. The equipment used for hydrogen permeation measurement is typically expensive and requires regular calibration and maintenance. Additionally, the test conditions and parameters must be carefully controlled to ensure accurate and reproducible results.
Despite these limitations, hydrogen permeation measurement is a valuable technique for evaluating the risk of hydrogen-induced cracking in the oil and gas industry. This method can be used to evaluate the performance of materials and coatings under realistic conditions, and to optimize corrosion control strategies to minimize the risk of hydrogen-induced cracking. Hydrogen permeation measurement is often used in combination with other corrosion monitoring techniques, such as weight loss measurement and electrochemical techniques, to provide a more comprehensive understanding of the corrosion process.
Ultrasonic thickness measurement
Ultrasonic thickness measurement is a widely used technique for monitoring corrosion rates in the oil and gas industry. This method involves using ultrasonic waves to measure the thickness of a metal coupon or structure, and then comparing the thickness measurements over time to evaluate the corrosion rate.
The principle behind this method is that as a metal corrodes, its thickness decreases, which can be detected using ultrasonic waves. The equipment used for ultrasonic thickness measurement typically consists of a handheld probe, which emits and receives ultrasonic waves, and a digital display or data logger, which displays the thickness measurements.
Ultrasonic thickness measurement is a non-destructive and non-intrusive technique, which makes it a convenient and safe method for monitoring corrosion rates. This method is also less affected by environmental factors, such as temperature and composition, compared to other corrosion monitoring techniques, such as weight loss measurement.
However, ultrasonic thickness measurement has its limitations in terms of the accuracy of the corrosion rate calculation. This method may not detect localized corrosion, such as pitting, and the thickness measurements may be affected by the geometry and surface finish of the metal coupon or structure. Additionally, this method cannot provide insights into the corrosion mechanism or the effects of environmental factors on the corrosion process.
Despite these limitations, ultrasonic thickness measurement is a valuable technique for monitoring corrosion rates in the oil and gas industry. This method can be used to provide real-time monitoring of the thickness of pipelines, tanks, and other equipment, to identify areas of high corrosion rates, and to optimize corrosion control strategies. Ultrasonic thickness measurement is often used in combination with other corrosion monitoring techniques, such as weight loss measurement and electrochemical techniques, to provide a more comprehensive understanding of the corrosion process.
Visual inspection methods
Visual inspection methods are the oldest and most common techniques for monitoring corrosion rates in the oil and gas industry. This method involves the direct observation of the metal surface, either through direct visual inspection or through the use of visual aids such as magnifying lenses or video cameras.
The principle behind this method is that as a metal corrodes, visible changes occur on the surface of the metal, such as discoloration, pitting, and scaling. These changes can be detected through visual inspection and can be used to evaluate the corrosion rate and the effectiveness of corrosion control strategies.
Visual inspection methods are inexpensive and easy to perform, making them a convenient and accessible technique for monitoring corrosion rates. This method is also less affected by environmental factors, such as temperature and composition, compared to other corrosion monitoring techniques.
However, visual inspection methods have their limitations in terms of the accuracy of the corrosion rate calculation. This method may not detect early stages of corrosion, where the changes are not visible to the naked eye, and may not be able to detect localized corrosion such as pitting, under coatings or within complex geometries. Additionally, visual inspection methods cannot provide insights into the corrosion mechanism or the effects of environmental factors on the corrosion process.
Despite these limitations, visual inspection methods are a valuable technique for monitoring corrosion rates in the oil and gas industry. This method can be used to identify areas of high corrosion rates, to evaluate the effectiveness of corrosion control strategies, and to guide more detailed and precise monitoring techniques. Visual inspection methods are often used in combination with other corrosion monitoring techniques, such as weight loss measurement, electrochemical techniques, and ultrasonic thickness measurement, to provide a more comprehensive understanding of the corrosion process.
Click here for Weight loss measurement, Electrical resistance measurement, Linear polarization resistance measurement
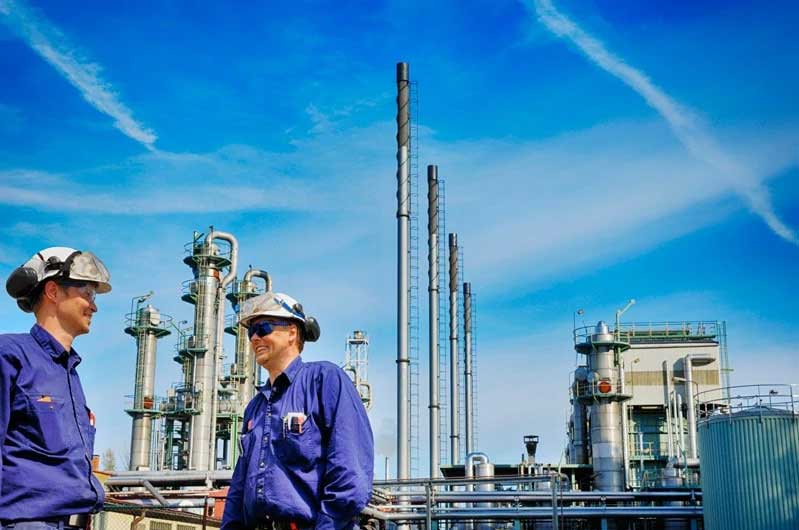
Contact us
Crystal Industrial Syndicate Pvt Ltd.
Phone : +91-22-27563850
Fax: +91-22-67939439
www.crystalindustrial.in
sales@crystalindustrial.in
Crystal Industrial Syndicate from India, manufactures a variety of corrosion coupons for a range of industrial processes. Our world-class corrosion coupons manufactured in India comply with the world’s most stringent certifications. We have clients the world, from Europe and North America to Africa and the Middle East. Please contact us for details about how we can meet your corrosion coupon requirements. Contact us
Copyright © 2023 by Crystal Industrial Syndicate Pvt Ltd. All rights reserved. www.crystalindustrial.in