How corrosion coupon test results help optimize corrosion inhibitor programs
Corrosion inhibitors are a common method for mitigating corrosion in industrial settings. These chemicals work by forming a protective layer on metal surfaces, preventing corrosive agents from coming into contact with the metal. However, simply adding corrosion inhibitors to a process stream is not always enough to prevent corrosion. It is important to optimize corrosion inhibitor programs to ensure that they are effective and efficient.
Optimizing corrosion inhibitor programs involves several steps. First, it is important to select the right corrosion inhibitor for the specific application. This may involve considering factors such as the type of metal being protected, the corrosive agents present in the process stream, and the temperature and pressure of the system.
Once the appropriate corrosion inhibitor has been selected, it is important to determine the optimal dosage and application method. Too little corrosion inhibitor may not provide adequate protection, while too much can be wasteful and expensive. The application method, such as injection quills or spray nozzles, can also impact the effectiveness of the corrosion inhibitor.
Regular monitoring and testing of the process stream can help ensure that the corrosion inhibitor program is working as intended. Corrosion coupon testing can help determine if the corrosion inhibitor is effective in preventing corrosion, and can also help identify areas where additional corrosion inhibitor may be needed.
In addition to monitoring and testing, it is important to maintain and replenish the corrosion inhibitor program regularly. Corrosion inhibitors can break down over time or become depleted, so it is important to follow a maintenance schedule that ensures the corrosion inhibitor program remains effective.
By optimizing corrosion inhibitor programs, you can prevent corrosion and extend the lifespan of your equipment. This can reduce maintenance costs, prevent downtime, and improve overall efficiency and productivity. Regular monitoring and maintenance can help ensure that your corrosion inhibitor program is effective and efficient for years to come.
How corrosion coupon test results help improve product quality
Corrosion can impact the quality of the products produced in industrial processes. When metal components corrode, they can introduce contaminants into the process stream, leading to product defects or failures. Corrosion can also cause equipment failures, which can result in lost product and production time. By managing corrosion, you can improve product quality and reduce waste.
Improving product quality through corrosion management involves several steps. First, it is important to identify areas where corrosion may be impacting product quality. This may involve analyzing product quality data, reviewing inspection reports, or conducting a risk assessment.
Once areas of concern have been identified, steps can be taken to mitigate corrosion and prevent product contamination. This may involve implementing corrosion inhibitor programs or improving water treatment processes to reduce corrosive agents in the process stream. Coatings or linings may also be applied to metal components to protect them from corrosion and prevent product contamination.
Regular monitoring and testing can help ensure that product quality is maintained. This may involve regular inspection of equipment, as well as testing of the process stream and product samples for contaminants.
By improving product quality through corrosion management, you can reduce waste and improve efficiency. Higher quality products are less likely to fail or be rejected, reducing the need for rework or additional production. This can save time and money, as well as improve customer satisfaction and loyalty.
Managing corrosion can also help reduce the risk of equipment failures, which can impact product quality and lead to lost production time. By addressing corrosion before it causes equipment failures, you can prevent product defects and improve overall productivity.
In summary, improving product quality through corrosion management involves identifying areas of concern, implementing corrosion mitigation strategies, and regular monitoring and testing. By managing corrosion, you can reduce waste, improve efficiency, and maintain high product quality.
How corrosion coupon test results help reduce maintenance costs
Corrosion can be a significant driver of maintenance costs in industrial processes. When metal components corrode, they may need to be repaired or replaced, which can be time-consuming and expensive. By reducing corrosion, you can reduce maintenance costs and improve efficiency.
Reducing maintenance costs through corrosion management involves several steps. First, it is important to identify areas where corrosion may be impacting equipment reliability and maintenance costs. This may involve analyzing maintenance data, reviewing inspection reports, or conducting a risk assessment.
Once areas of concern have been identified, steps can be taken to mitigate corrosion and prevent equipment failures. This may involve implementing corrosion inhibitor programs or improving water treatment processes to reduce corrosive agents in the process stream. Coatings or linings may also be applied to metal components to protect them from corrosion.
Regular monitoring and testing can help ensure that corrosion is being effectively managed and maintenance costs are being reduced. This may involve regular inspection of equipment, as well as testing of the process stream and equipment components for corrosion.
By reducing maintenance costs through corrosion management, you can improve the efficiency and productivity of your operation. By preventing equipment failures and reducing the need for repairs and replacements, you can reduce downtime and improve overall equipment reliability. This can save time and money, as well as improve customer satisfaction and loyalty.
In summary, reducing maintenance costs through corrosion management involves identifying areas of concern, implementing corrosion mitigation strategies, and regular monitoring and testing. By managing corrosion, you can reduce maintenance costs, improve efficiency, and maintain high equipment reliability.
Click here for details on how corrosion coupon test results help in identifying problematic areas and improving equipment lifespan
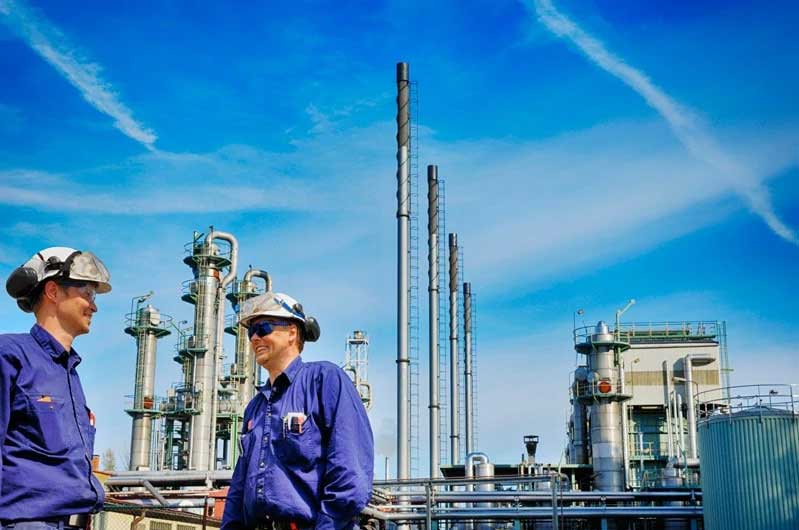
Contact us
Crystal Industrial Syndicate
Phone : +91-22-27563850
Fax: +91-22-67939439
www.crystalindustrial.in
sales@crystalindustrial.in
Crystal Industrial Syndicate from India, manufactures a variety of custom injection quills for a range of industrial processes. Our world-class chemical injection quills are manufactured in India comply with the world’s most stringent certifications. We have clients around the world, from Europe and North America to Africa and the Middle East. Please contact us for details about how we can meet your injection quills requirements. Contact us
Copyright © 2023 by Crystal Industrial Syndicate Pvt Ltd. All rights reserved. www.crystalindustrial.in