The aerospace industry uses corrosion coupons to monitor the performance of coatings and materials used in aircraft components. The performance of these coatings and materials is critical to ensure the safety and reliability of aircraft components and to extend their useful life.
Corrosion coupons are installed in aircraft components and left in place for a predetermined amount of time. After retrieval, the coupons are analyzed to determine the extent of corrosion on the coupon surface. By comparing the corrosion rates of coated and uncoated coupons, aerospace manufacturers can evaluate the effectiveness of the coatings and materials used in the aircraft components.
This information can be used to optimize the use of coatings and materials, to identify areas of high corrosion rates, and to take corrective actions to prevent equipment failure, reduce maintenance costs, and ensure the reliable and safe operation of the aircraft. By optimizing the use of coatings and materials, aerospace manufacturers can reduce the weight of the aircraft, improve its aerodynamics, and increase fuel efficiency.
The use of corrosion coupons in the aerospace industry is critical to comply with regulatory requirements for monitoring and reporting of coating performance in aircraft components. It also helps to identify areas of high corrosion rates and to take corrective actions to prevent equipment failure and ensure the safety and reliability of the aircraft.
The different aircraft components that benefit from corrosion coupon monitoring include landing gear, engine components, structural components, and other critical components. By utilizing corrosion coupons in these components, aerospace manufacturers can maintain the integrity of their aircraft, reduce downtime, and ensure the safety of their passengers and crew.
Corrosion monitoring in aircraft
Corrosion monitoring is a critical component of aircraft maintenance and safety. Corrosion can weaken aircraft components and compromise their structural integrity, which can lead to catastrophic failure. Corrosion monitoring in aircraft involves the use of various techniques to detect, measure, and prevent corrosion.
One of the most commonly used techniques for corrosion monitoring in aircraft is the use of corrosion coupons. Corrosion coupons are installed in aircraft components and left in place for a predetermined amount of time. After retrieval, the coupons are analyzed to determine the extent of corrosion on the coupon surface. By comparing the corrosion rates of coated and uncoated coupons, aerospace manufacturers can evaluate the effectiveness of the coatings and materials used in the aircraft components.
Other techniques used for corrosion monitoring in aircraft include visual inspections, eddy current testing, ultrasonic testing, and X-ray inspection. Visual inspections involve a visual examination of the aircraft components to identify signs of corrosion, such as discoloration or pitting. Eddy current testing and ultrasonic testing use electromagnetic waves or sound waves to detect corrosion on the surface or subsurface of the aircraft components. X-ray inspection involves the use of X-rays to detect corrosion in inaccessible areas of the aircraft components.
Corrosion monitoring in aircraft is critical to ensure the safety and reliability of the aircraft. It is also necessary to comply with regulatory requirements for monitoring and reporting of corrosion rates in aircraft components. By monitoring and controlling the corrosion rate in aircraft components, aerospace manufacturers can maintain the integrity of their aircraft, reduce downtime, and ensure the safety of their passengers and crew.
How corrosion affects the maintenance process of aircraft parts
Corrosion can have a significant impact on the maintenance process of aircraft parts. The presence of corrosion on aircraft components can weaken the structural integrity of these components, which can result in catastrophic failure if left unaddressed. Therefore, it is critical to identify and address any corrosion on aircraft components as soon as possible.
The presence of corrosion on aircraft components can complicate the maintenance process by requiring additional steps to address the corrosion. These additional steps can increase the time and cost of maintenance, as well as the downtime of the aircraft. For example, if corrosion is identified on an aircraft component, the component may need to be removed and cleaned to remove the corrosion before it can be repaired or replaced. This additional step can add significant time and cost to the maintenance process.
Corrosion can also affect the lifespan of aircraft components. If corrosion is not identified and addressed, it can continue to weaken the structural integrity of the component over time, which can shorten its lifespan. This can lead to more frequent maintenance and replacement of these components, which can increase the overall cost of aircraft maintenance.
To mitigate the impact of corrosion on aircraft maintenance, it is important to implement a comprehensive corrosion monitoring and prevention program. This program should include regular inspections of aircraft components, the use of corrosion-resistant materials and coatings, and the use of corrosion inhibitors. By addressing corrosion early and preventing its occurrence, aerospace manufacturers can reduce the impact of corrosion on the maintenance process of their aircraft components.
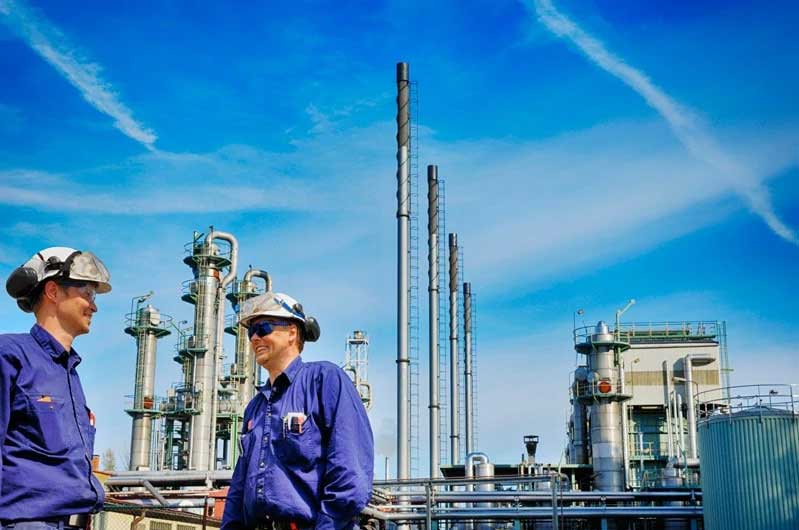
Contact us
Crystal Industrial Syndicate Pvt Ltd.
Phone : +91-22-27563850
Fax: +91-22-67939439
www.crystalindustrial.in
sales@crystalindustrial.in
Crystal Industrial Syndicate from India, manufactures a variety of corrosion coupons for a range of industrial processes. Our world-class corrosion coupons manufactured in India comply with the world’s most stringent certifications. We have clients the world, from Europe and North America to Africa and the Middle East. Please contact us for details about how we can meet your corrosion coupon requirements. Contact us
Copyright © 2023 by Crystal Industrial Syndicate Pvt Ltd. All rights reserved. www.crystalindustrial.in