Corrosion measurements are critical in the oil and gas industry as corrosion can cause equipment failure, leaks, and environmental damage. There are several types of corrosion measurements used in the industry, including:
- Weight loss measurement: This is the most basic and oldest method of measuring corrosion. It involves weighing a metal coupon before and after exposure to the corrosive environment, and the difference in weight is used to calculate the corrosion rate.
- Electrical resistance measurement: This method involves measuring the change in electrical resistance of a metal coupon as it corrodes. The corrosion rate is then calculated based on the change in resistance.
- Linear polarization resistance measurement: This method involves applying a small electrical potential to a metal coupon and measuring the resulting current flow. The corrosion rate is then calculated based on the resistance to current flow.
- Electrochemical impedance spectroscopy: This method involves applying an AC electrical signal to a metal coupon and measuring the resulting electrical response. The response is analyzed to determine the corrosion rate and the properties of the corroding system.
- Hydrogen permeation measurement: This method involves measuring the amount of hydrogen that diffuses through a metal coupon as it corrodes. The corrosion rate is then calculated based on the amount of hydrogen permeation.
- Ultrasonic thickness measurement: This method involves measuring the thickness of a metal component over time to determine the rate of corrosion.
- Visual inspection: Visual inspection can be used to identify visible signs of corrosion, such as pitting or discoloration, on metal components. This method is often used in conjunction with other corrosion measurements to provide a complete picture of the corrosion process.
These corrosion measurement techniques can be used in a variety of ways to monitor corrosion in the oil and gas industry, including in pipelines, tanks, and other equipment.
Weight loss measurement
Weight loss measurement is a common and widely used method of measuring corrosion rates in the oil and gas industry. This method involves exposing a metal coupon, a small piece of metal that is representative of the material being used in equipment or pipelines, to a corrosive environment for a specific amount of time. The coupon is then removed and cleaned, and the change in weight is measured. The difference in weight is used to calculate the corrosion rate.
This method is relatively simple and inexpensive, and it can be used to monitor corrosion rates over a wide range of conditions. However, weight loss measurements can be affected by factors such as the exposure time, the temperature, and the composition of the environment, which can affect the accuracy of the corrosion rate calculation.
Weight loss measurement is often used in combination with other corrosion monitoring techniques, such as electrochemical methods, to provide a more complete picture of the corrosion process. It is commonly used in the oil and gas industry to monitor the corrosion rates of pipelines, storage tanks, and other equipment, and to determine the effectiveness of corrosion inhibitors and other protective coatings.
Overall, weight loss measurement is a valuable and widely used method of measuring corrosion rates in the oil and gas industry, but it has its limitations and is often used in conjunction with other techniques to provide a more accurate and complete picture of the corrosion process.
Electrical resistance measurement
Electrical resistance measurement is a corrosion monitoring technique commonly used in the oil and gas industry. This method involves attaching a pair of electrodes to a metal coupon, which is then exposed to a corrosive environment for a specified period of time. The electrical resistance of the coupon is measured at regular intervals during the exposure period, and the change in resistance over time is used to calculate the corrosion rate.
The principle behind this method is that as a metal corrodes, its electrical resistance changes due to the changes in the metal’s properties. The change in resistance is proportional to the rate of corrosion, and can be used to calculate the corrosion rate.
Electrical resistance measurement is a simple and cost-effective method of monitoring corrosion rates, and can provide continuous monitoring of corrosion rates over time. It is also less affected by factors such as temperature and composition of the environment compared to other techniques, such as weight loss measurement.
However, electrical resistance measurement has limitations in terms of the accuracy of the corrosion rate calculation, as the relationship between electrical resistance and corrosion rate is not always linear, and the geometry of the metal coupon can affect the resistance measurement.
Despite these limitations, electrical resistance measurement is a widely used technique in the oil and gas industry for monitoring corrosion rates, and can be used to determine the effectiveness of corrosion inhibitors and other protective coatings. It is often used in combination with other corrosion monitoring techniques to provide a more comprehensive understanding of the corrosion process.
Linear polarization resistance measurement
Linear polarization resistance measurement is a widely used corrosion monitoring technique in the oil and gas industry. This method involves applying a small electrical potential to a metal coupon, which is immersed in a corrosive environment. The resulting current flow is measured, and the polarization resistance of the metal coupon is calculated. The polarization resistance is proportional to the corrosion rate, which can then be calculated based on the resistance measurement.
The principle behind this method is that as a metal corrodes, its electrical properties change, which affects the current flow and the polarization resistance of the metal. The change in polarization resistance is proportional to the corrosion rate, and can be used to calculate the rate of corrosion.
Linear polarization resistance measurement is a simple and cost-effective method of monitoring corrosion rates, and can provide continuous monitoring of corrosion rates over time. This method is less affected by environmental factors such as temperature and composition of the environment, compared to other corrosion monitoring techniques such as weight loss measurement.
However, linear polarization resistance measurement has its limitations in terms of the accuracy of the corrosion rate calculation. The relationship between polarization resistance and corrosion rate is not always linear, and the geometry of the metal coupon can affect the resistance measurement. Additionally, the method is less sensitive to localized corrosion, such as pitting, compared to other techniques such as electrochemical impedance spectroscopy.
Despite these limitations, linear polarization resistance measurement is a widely used technique in the oil and gas industry for monitoring corrosion rates, and can be used to determine the effectiveness of corrosion inhibitors and other protective coatings. It is often used in combination with other corrosion monitoring techniques to provide a more comprehensive understanding of the corrosion process.
Click here for Electrochemical impedance spectroscopy, Hydrogen permeation measurement, Ultrasonic thickness measurement, Visual inspection.
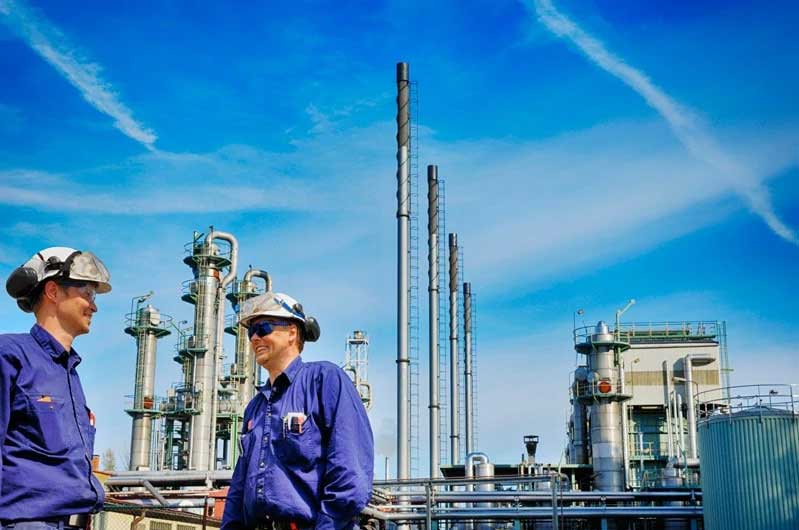
Contact us
Crystal Industrial Syndicate Pvt Ltd.
Phone : +91-22-27563850
Fax: +91-22-67939439
www.crystalindustrial.in
sales@crystalindustrial.in
Crystal Industrial Syndicate from India, manufactures a variety of corrosion coupons for a range of industrial processes. Our world-class corrosion coupons manufactured in India comply with the world’s most stringent certifications. We have clients the world, from Europe and North America to Africa and the Middle East. Please contact us for details about how we can meet your corrosion coupon requirements. Contact us
Copyright © 2023 by Crystal Industrial Syndicate Pvt Ltd. All rights reserved. www.crystalindustrial.in