Here are some possible problems or mistakes that can occur during the installation, use, and maintenance of corrosion coupons:
- Improper installation: If the coupons are not installed correctly, they may not be in contact with the corrosive environment they are meant to monitor, leading to incorrect readings.
- Contamination: Coupons may become contaminated with dirt, debris or other materials, affecting the accuracy of the corrosion rate measurement.
- Sampling error: Sampling the coupons at incorrect intervals or for an incorrect duration can lead to incorrect results.
- Improper handling and storage: Coupons may be damaged or contaminated during removal, storage or transport, affecting the accuracy of the measurements.
- Lack of standardization: Coupons from different manufacturers may have different dimensions, thickness, or compositions, leading to difficulties in comparing results from different coupons.
- Inadequate data analysis: Incorrect analysis of coupon data can lead to incorrect conclusions about the extent and causes of corrosion.
- Improper maintenance: Coupons may become damaged or otherwise affected if not properly maintained or stored.
It is important to carefully follow the manufacturer’s instructions and industry standards for the proper installation, use, and maintenance of corrosion coupons to avoid these potential problems and ensure accurate and reliable results.
Mistake # 1. Improper installation
Improper installation is one of the common problems that can occur during the use of corrosion coupons. Proper installation is crucial to ensure that the coupons are in contact with the corrosive environment they are meant to monitor, so that accurate readings can be obtained.
If the coupons are not installed correctly, they may not be exposed to the full range of corrosive conditions, leading to incorrect readings. For example, if the coupon is not installed in the right orientation or if it is installed too close to a non-corrosive material, the corrosion rate may not accurately reflect the conditions of the environment being monitored.
To avoid this problem, it is important to follow the manufacturer’s instructions for the correct installation of the coupons, including the correct orientation and location of the coupons, and to take into account any specific requirements for the application, such as immersion depth, temperature, and exposure time.
By ensuring proper installation, the results obtained from corrosion coupons can provide accurate information about the extent and causes of corrosion, which can be used to make informed decisions about the management and mitigation of corrosion.
Mistake # 2. Contamination
Contamination is another common problem that can occur during the use of corrosion coupons. Coupons may become contaminated with dirt, debris, or other materials, which can affect the accuracy of the corrosion rate measurement.
For example, if debris accumulates on the surface of the coupon, it can create a barrier that prevents the corrosive environment from coming into direct contact with the coupon. This can result in an underestimation of the corrosion rate, as the coupon may not be fully exposed to the corrosive conditions.
Similarly, if a coupon becomes contaminated with a material that is not corrosive, the results may be skewed, leading to incorrect conclusions about the extent and causes of corrosion.
To avoid contamination, it is important to handle and store the coupons carefully, taking precautions to prevent any exposure to dirt, debris, or other contaminants. Coupons should also be cleaned thoroughly before and after removal, to ensure that they are free from any contaminants that may affect the accuracy of the results.
By taking steps to prevent contamination, the results obtained from corrosion coupons can provide accurate and reliable information about the extent and causes of corrosion, which can be used to make informed decisions about the management and mitigation of corrosion.
Mistake # 3. Sampling error
Sampling error is another potential problem that can occur when using corrosion coupons. Sampling the coupons at incorrect intervals or for an incorrect duration can lead to incorrect results and inaccurate conclusions about the extent and causes of corrosion.
For example, if the coupons are removed too frequently, the corrosion rate may be underestimated, as the coupon may not have been exposed to the corrosive environment for a sufficient amount of time. Conversely, if the coupons are left in place for too long, the corrosion rate may be overestimated, as the coupon may have been exposed to corrosive conditions for a longer duration than is representative of the actual conditions in the environment.
To minimize sampling error, it is important to follow established industry standards and the manufacturer’s instructions for the frequency and duration of coupon removal. Sampling intervals should be chosen based on the rate of corrosion, the nature of the corrosive environment, and other relevant factors.
By carefully controlling the sampling process, the results obtained from corrosion coupons can provide accurate and reliable information about the extent and causes of corrosion, which can be used to make informed decisions about the management and mitigation of corrosion.
Click here for improper handling and storage, lack of standardization, inadequate data analysis, improper maintenance
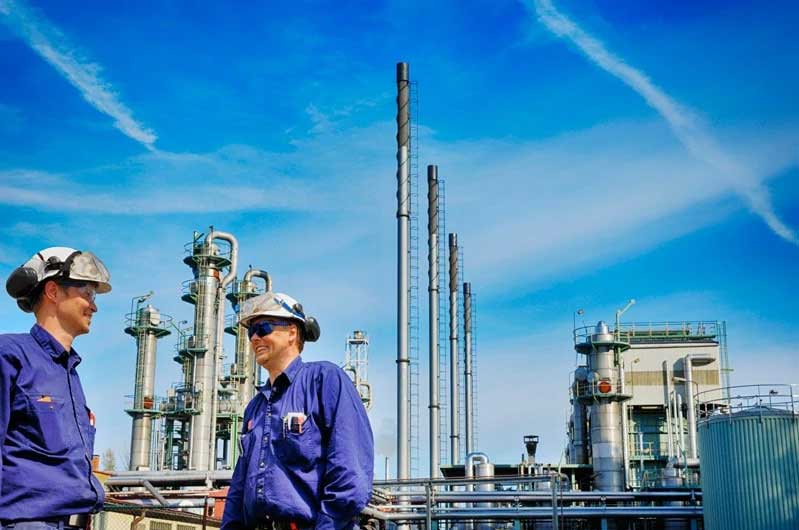
Contact us
Crystal Industrial Syndicate Pvt Ltd.
Phone : +91-22-27563850
Fax: +91-22-67939439
www.crystalindustrial.in
sales@crystalindustrial.in
Crystal Industrial Syndicate from India, manufactures a variety of corrosion coupons for a range of industrial processes. Our world-class corrosion coupons manufactured in India comply with the world’s most stringent certifications. We have clients the world, from Europe and North America to Africa and the Middle East. Please contact us for details about how we can meet your corrosion coupon requirements. Contact us
Copyright © 2023 by Crystal Industrial Syndicate Pvt Ltd. All rights reserved. www.crystalindustrial.in